A piston ring is a split ring that fits into a groove on the outer diameter of a piston in a reciprocating engine such as an internal combustion engine or steam engine.
The main functions of piston rings in reciprocating engines are:
-
Sealing the combustion chamber so that there is minimal loss of gases to the crank case.
-
Improving heat transfer from the piston to the cylinder wall.
-
Maintaining the proper quantity of the oil between the piston and the cylinder wall
-
Regulating engine oil consumption by scraping oil from the cylinder walls back to the sump.
The gap in the piston ring compresses to a few thousandths of an inch when inside the cylinder bore. Piston rings are a major factor in identifying if an engine is two stroke or four stroke. Three piston rings suggest that it is a four stroke engine while two piston rings suggest that it is a two stroke engine. Most piston rings are made of a very hard and somewhat brittle cast iron.
Piston Ring Types
Compression Rings
The main functions of compression rings are to seal the combustion chamber from the crankcase and transfer heat from the piston to the cylinder. However, they also play an important part in controlling engine oil consumption.
There are the following types:

A piston ring with a rectangular cross section. This ring with its geometrically simple shape performs the necessary sealing functions under normal operating conditions. With a peripheral coating and appropriate barrel face the rectangular ring is today used mainly in the top groove in passenger car gasoline and diesel engines. Besides service in internal combustion engines, rectangular rings are commonly used as rotary shaft seals, e.g. transmission seals

Owing to the tapered running face the ring contacts the cylinder bore with its bottom outer edge. This shortens running-in and improves oil scraping. The gas forces acting initially at the running face provide a degree of pressure relief (especially when used in the top groove). Taper faced rings are chiefly installed in the second groove in passenger car gasoline and passenger car and truck diesel engines. In passenger car gasoline engines they are also used in the top groove.
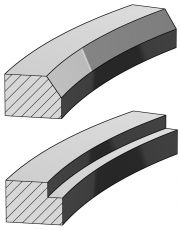
By providing an edge relief on the top side of rectangular and taper faced rings a twist effect is achieved which, in all operating phases without gas pressure loading, brings the ring into bore contact only with its bottom outer edge while the inner edge contacts the bottom groove side (positive twist). This helps to improve oil consumption control. Under operating conditions the gas pressure forces the ring flat against the piston groove, creating an additional dynamic behaviour of the ring
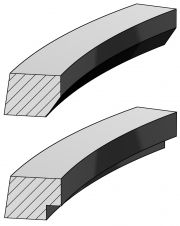
In the installed condition this edge relief causes a negative twist, i.e. in the opposite direction to a ring with the relief on the top side. The taper must be larger than on a taper faced ring without twist or with positive twist so that the top outer edge is prevented from contacting the cylinder wall. The effect of the negative twist is to make the ring contact the groove and create a seal with its outer bottom side and its inner top side
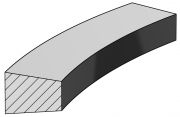
A compression ring with a wedge cross section. With its tapered sides, radial movement of the ring in engine operation will cause the axial clearance in the groove to increase and decrease. This greatly reduces ring sticking, as the ring continuously works its way free of the combustion residues. These rings are designed with an overall side angle of 6° bzw. 15°, the larger angle being more effective against the tendency to coking.

A compression ring with only the top side tapered. Like on the keystone ring, the tapered side (keystone angle 7°) causes the axial clearance to vary as the ring moves radially, and thus reduces ring sticking. Owing to its asymmetrical cross section the ring has a positive twist when installed. A half keystone ring is used in the top groove of passenger car and truck diesel engines when a rectangular ring is no longer adequate in regard to ring sticking but a keystone ring is not yet warranted.

This ring is used mainly in small 2-stroke gasoline engines as a "head land" ring, the vertical arm of the L being flush with the top edge of the piston crown [9]. With gas pressure acting behind the vertical arm, this ring will also seal when in contact with the top side of the piston groove. Besides being used in 2-stroke engines, in some cases it has been installed in automotive diesel engines in order to minimize crevice volume in the combustion chamber
Scraper Rings
Practically all of the scraper rings used are rings with a step recessed into the bottom outer face. This assures extremely effective oil scraping
The following types exist:
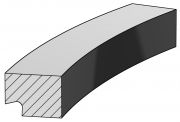
This can be installed in the second groove in passenger car gasoline and passenger car and truck diesel engines, but has been almost entirely replaced by the taper faced Napier ring. It is now occasionally used only in the compressors of air brake systems.
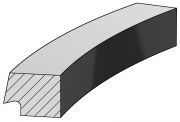
Like on the taper faced ring, the periphery of this ring is designed with a taper in order to improve oil scraping and quicken running-in. These rings are used on the same applications as Napier rings.

On this ring the step runs out at the gap and is designed without an undercut. It seals better against blowby than the Napier and taper faced Napier rings with a continuous step. The applications for this ring are the same as for Napier and taper faced Napier rings.

A slotted oil control ring with two outer lands, the sides of which are parallel to one another. As the width of the lands is smaller than the overall width a higher unit pressure can be obtained than with a rectangular ring.
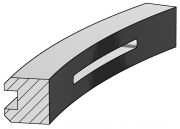
To obtain still higher unit pressures than with a slotted oil control ring, this type of ring has the outer lands chamfered on the outer edge.
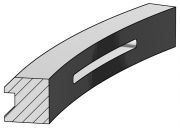
On this type both lands are chamfered on the edge facing the combustion chamber. While the unit pressure is the same, oil consumption is reduced through the improved oil scraping effect.
Oil Control Rings
The main function of the rings in the bottom piston groove is to scrape oil from the cylinder wall, i.e. oil control rings play a major part in regulating the oil economy of the internal combustion engine. In order to control lube oil consumption most effectively, various types of oil rings are available depending on the application.
Single-Piece Oil Control Rings
Single-piece oil control rings - like for example compression rings - derive their tangential forcefrom their inherent inner tension. There are the following types:

A slotted oil control ring with two outer lands, the sides of which are parallel to one another. As the width of the lands is smaller than the overall width a higher unit pressure can be obtained than with a rectangular ring.
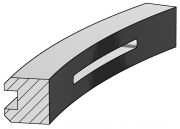
To obtain still higher unit pressures than with a slotted oil control ring, this type of ring has the outer lands chamfered on the outer edge.
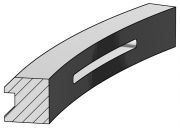
On this type both lands are chamfered on the edge facing the combustion chamber. While the unit pressure is the same, oil consumption is reduced through the improved oil scraping effect.
Two-Piece Oil Control Rings
Two-piece oil control rings consist of a cast iron or profiled steel ring and a coil spring.
There are the following types:
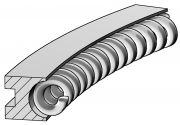
A slotted oil control ring with two outer lands, the sides of which are parallel to one another. Compared to the slotted oil control ring described above, this ring additionally has a groove on the inside diameter to accommodate the coil spring.
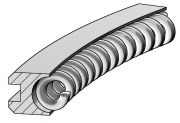
Consists of a ring similar to the bevelled edge ring, but has an additional groove for the coil spring.
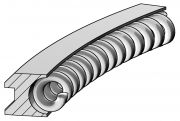
Like the double bevelled ring, but with a groove to hold the coil spring.

The wear coating gives the ring high long-time stability and makes it particularly suitable for operation mainly in diesel engines. The profile grinding of the lands allows close tolerances to be achieved on these critical working surfaces.

A bevelled edge ring made from a high-chromium profiled steel. Wear protection is provided by nitriding the ring all over. Like the chromed bevelled edge ring, this ring is chiefly used in diesel engines. Oil drainage is provided by means of punched holes.